In the freight world, delays are inevitable. Everything could be running smoothly for the first leg of a shipment when all of the sudden inclement weather shuts a driver down. While we may do everything in our power to get our shipments delivered on time, there are many things that we can’t control that can contribute to late shipments. The key to minimizing these problems is not to try to control the uncontrollable, but rather to plan ahead and manage every situation effectively when something undesirable occurs.
The first step in managing the unexpected is to pay attention to the details involved with every shipment. Know where the shipment is delivering and when it is needed by. Warehouse requirements should always be known ahead of time to limit the chance that the freight will be rejected when it arrives. Dispatchers can even check the weather forecasts along the route to try to minimize the risk of running into weather delays. They can’t control the weather, but they can try to find the path of least resistance. With every shipment, we must expect that there will be potential delays somewhere during transit. Instead of becoming frustrated that the delays occurred, it is important to have a plan of action in place for when they happen.
Much like in every industry, problems are going to occur if you are shipping multiple truckloads or multiple LTL shipments every day. It is important to keep a positive mindset, hoping for the best for every shipment, but to be realistic and do everything that you can to be prepared for the worst-case scenario. A shipment isn’t complete just because you booked the load – it is vital to have a plan B, plan C, and even plan D in place for the possibility of a casualty occurring. When you learn to plan ahead, you won’t be blindsided by a casualty. You’ll be able to take action and fix the problem, keeping your customer happy and your company profitable. To see how we can help you with managing the unexpected, start today with Zip Xpress!
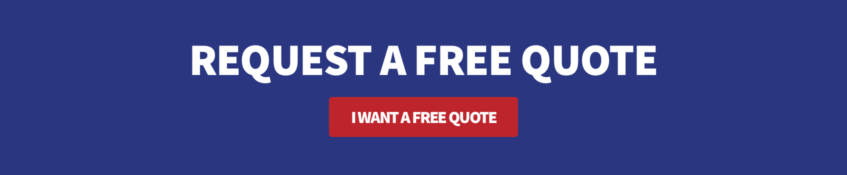